Plastic Injection Molding
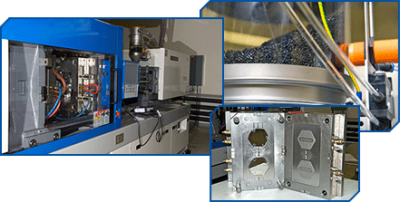
Jatco experience and state-of-the-art equipment produce the finest products efficiently and economically. We bring a problem-solving mindset and love to find creative solutions to your manufacturing challenge. Our injection molding consultants are here to help you with everything you need including design, production, packaging, product storage and distribution. Call us today at 209-497-4297 and let’s chat about your project.
With 25 presses, ranging from 55 to 1500 tons, all equipped with robotics (most with 3-axis servo robot capability), handle operations from small to large, including complex, multi-component products. We routinely handle molds weighing up to 20,000 pounds.
Jatco technology advantages ensure consistent, reliable product:
Call our Director of Sales Steven Ames and get your quote today 209-497-4290.
Technology drives all that we do at Jatco. All of our presses are equipped with robotics, most with 3 axis servo robot capability to handle the most complex molding operations.
Our engineers focus heavily on “design for manufacturability”. This is the process of developing production techniques and overall production architecture so that large runs can be done economically with high quality, and are easy to revisit when there is a need to produce additional runs in the future. We focus extensively on a production flow that will manufacture your product(s) at a very good cost, high quality, and are always ready for second runs. Contact us today to discuss your project.
We are one of very few plastic production companies with ANAB certification (ANAB stands for ANSI National Accreditation Board). This certification assures our customers that they will be working with highly competent team that fully understands production, quality measurements, and can meet all other requirements for your product(s). In order to get ANAB certified our team has gone through extensive training, practice and documentation. We are one of the few injection molding companies that bring this to table.
JATCO offers a variety of molds that are specifically designed for different types of injection molding runs. Here are the different types of molds we offer as well as their strengths and weaknesses. When working with JATCO our specialists and engineers will advise you on the best option for your own production line.
Class 101: 1 Million Shots/Cycles
Built for extremely high production. This is the highest standard mold built with the hardest steel that takes the longest to burn/cut. It contains the highest quality components and is the highest relative cost mold.
Class 102: 500K Shots/Cycles
Medium to high production mold that is good for abrasive materials and/or parts requiring tighter tolerances. This is a higher quality mold that is still higher in cost.
Class 103: 250K Shots/Cycles
Medium production mold and perhaps the most common mold for low to medium production needs. Unless specified, many molders/mold makers quote and build to this specification; however, Jatco ALWAYS communicates and confirms this requirement with our customer for every part.
Class 104: Under 100K Shots/Cycles
Low production mold that is used for limited production and preferably with non-abrasive material.
Class 105: Not Exceeding 500 (Prototype Only)
This classification is for prototype molds with very limited life expectancy. Some can be as low as 10-25 part (rubber molds) or up to 500. They are constructed using a variety of potential materials depending upon the need of the customer.
About Jatco
JATCO is a Northern California plastics manufacturer who is knowns as a global leader in plastic injection molding. We are a one stop shop which offers plastics product (life) consulting, plastics design, plastics production, warehousing and distribution solutions for just about any project.
JATCO CONTACT INFORMATION
Our Headquarters address is:
Jatco Incorporated
4801 Stoddard Road
Modesto, CA 95356 USA, U.S.A.
Tel: 209.497.4297
Fax: 510.4871880
Also visit our other sites (click below): TestCylinderMolds for test cylinders
Plantway for plant trays